The Future of Industrial/Scientific-Grade Image-Processing Board Technology
By Barry Mazor
The Participants:
• Phil Colet, Director of Sales & Mktg., Coreco. (St. Laurent, QC, Canada)
• George Blackwell, Sr. Manager of End- User Marketing, Cognex. (Natick, MA)
• John Hotchkiss, Product Mktg. Mgr., Imaging Products, Data Translation. (Marlboro, MA)
• Pierantonio Boriero, Product Line Mgr., Matrox Imaging. (Dorval, QC, Canada)
• John Morrissey, President & COO, MuTech. (N. Billerica, MA)
• Jeff Wilson, Sales & Marketing VP, Treasurer & CFO, BitFlow. (Woburn, MA)
• Marc Damhaut, Marketing Manager, Euresys. (Angleur, Belgium)
• John Hanks, Analyst Software Prod. Mgr., National Instruments. (Austin, TX)
• Tony Molinari, VP Marketing & Business Development, Foresight Imaging.
(Chelmsford, MA)
• Brad Finney, Director of N. American Sales, Imaging Technology. (Bedford, MA)
• Richard Jaenicke, Director of Product Marketing, Mercury Computer Systems. (Chelmsford, MA)
|
All right…so what happens next?
Barry Mazor, Advanced Imaging: Assuming the picture of the scientific/industrial grade “imaging board” situation I’ve just spelled out is so (and if you don’t agree with that picture, please
tell us why!), where do you see frame grabbers and image-processing boards fitting into system solutions over the next 2-4 years?
|
Phil Colet, Coreco: To begin, let me say that I do agree with the statement that OEMs have been looking for workable tools instead of individual components, which gives us an indication of where frame grabbers
and image-processing boards are headed. OEMs will be looking for a product offering that gives them advantages in the marketplace–and component companies that can offer unique machine-vision algorithms, tightly-coupled acceleration
engines and shorter time to market, along with all of the frame grabber functions will be the successful players in tomorrow’s market.
From the hardware point of view, more and more "system"-related functions will continue to be integrated onto the machine-vision card.
For example, Coreco's current Viper series of frame grabbers combines image acquisition and pre-processing capability along with timing, control and I/O signals–all controlled from the card. This type of functional integration onto one
card will continue over the next four years.
And since a substantial investment of any machine-vision-based product is the software component, OEMs are seeking out solutions–and will continue to–that maximize their software Return on Investment (ROI). Simply put, this means
seeking solutions that will improve performance without re-deploying software development.
George Blackwell, Cognex: In the three- to four-year time frame,
we could see some digital connections to PCs that might begin to supplement–not replace–frame grabbers. Image acquisition for image processing boards will become more flexible. Factory-floor end-users will continue to prefer
image-processing boards or packaged vision systems to avoid the integration complexities and maintenance associated with frame-grabber-based systems.
Tony Molinari, Foresight Imaging: For our industrial and medical imaging markets, we see frame grabbers continuing to fit into system solutions in
ever-increasing numbers. These markets require images of high accuracy–results that cannot be delivered by low-cost multimedia boards. They also require the fastest delivery of images and video streams to system memory for processing by
the ever-improving CPU. With this increasing speed of CPUs, lower costs, easy programmability, and prevalent and low-cost multi- processor CPUs, we see image processing boards continuing to decline relative to frame grabbers in system
solutions. We also see users demanding more and more from frame grabbers!
One of these needs is video streaming. We are seeing more and more customers with diverse applications requiring high-speed video streaming. These streaming needs range from a few seconds up to a few minutes of high-accuracy video. We see
this going beyond a few minutes and to higher and higher frequencies, especially in medical imaging.
Brad Finney, Imaging Technology: I am excited by the introduction of those smart cameras and vision boxes. However,
I think that the original motivation of migrating to board-level products–to leverage the power and capabilities of the PC—
is still the dominating force. Smart cameras and vision boxes free up the host PC from vision duties, but generally introduce increased cost. I believe that they will have a very useful niche, but will not greatly effect how board-level
products fit into vision systems over the next 2-4 years.
As boring as it might sound, I think that frame grabbers and image processing boards, in that time frame, will be used in system solutions much the same way they are today! You described a major trend toward board-level products beginning
in 1986 fueled by the PC. That trend accelerated greatly with the introduction of the PCI bus (not to mention the Pentium).
So yes, there is new technology, IEEE-1394, with related smart cameras, etc., that is a force for change, but I do not believe that it will change the industry like we saw with the two examples above—even though I believe that IEEE-1394
will (barring any standards or licensing mishaps) gain strong acceptance in commercial applications and in some lower-end image analysis and machine-vision apps. But I don't believe that it has the feature set and performance capabilities
to replace board-level products, or that the feature set that will be available on commercial-grade vision products (like we see on some PCs and will certainly see on almost every PC in the future) satisfies the needs of the serious
machine-vision and image-analysis OEM.
John Hanks, National Instruments: National Instruments sees customers wanting solutions and flexibility, not raw image-acquisition hardware. Today, the PC is the most open and flexible platform for the integration of diverse I/O
such as vision, motion control, instrument control, networking, and so on. With PC performance continuing to improve as prices become cheaper, NI sees the PC continuing to be the platform of choice for measurement and automation
developers and machine builders.
For image acquisition hardware, we're focusing on making challenging imaging applications simple. Examples include making digital-camera-control software and cables to simplify control and connectivity, in part by helping to define
"Camera Link", a new multi-vendor connectivity standard for digital cameras. Image-acquisition hardware and digital cameras will continue to provide the most cutting-edge technology to acquire the largest images at the highest
frame rates. To facilitate customers locating solutions, NI, with our network of hundreds of system integrators, offers a wide range of unique solutions that addresses specific customers needs. These systems range from liquid crystal
display inspection to semiconductor wafer mapping to fiber optic alignment to chocolate candy inspection, and so on.
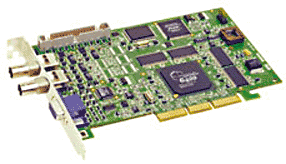
Pierantonio Boriero, Matrox Imaging: In its simplest form, the role of a frame grabber has been to capture raster images from a video source (such as a camera) into computer memory. This function is being re-defined, if not
eliminated, by the emergence of standard high-speed digital serial computer interfaces such as IEEE 1394 and USB 2.0. Although both standards can comfortably handle TV data rates, frame grabbers will still be required for high-resolution
and/or high-speed frame or line-scan cameras. Faster versions of these standards are planned but their adoption will take time due to inertia in the mainstream computing industry.
As for image-processing boards, the ever-increasing processing power and data throughput of host computers may appear
to cast a shadow on their future. It's true that many of the past applications that required the use of such boards can now be solved with software running on the host computer. However, new applications continually emerge that far exceed
the processing power and data throughput of even the most sophisticated multi-processor host computer. With input and processing requirements in the hundreds of Mpix/sec, dedicated image-processing boards are going to continue to offer
the best performance at the best price.
Jeff Wilson, Bitflow: I begin with the obvious: Our industry overwhelmingly prefers the personal computer as its image- processing system platform. Provided that the desired image can be acquired from the camera of choice, the PC
is the best way to go, with its low-cost, de facto standard development tools and image-processing software building blocks, a congenial debugging environment, implacable cost reduction and performance improvement, modular extendibility,
and tremendous choice.
But perhaps not so obviously, PCs don't cater to image processing and machine vision! We enjoy relentlessly-improving PCs only because mass markets such as word processing, Web browsing, teleconferencing, and computer gaming demand them.
Our relatively small imaging market segment takes advantage of whatever technical infrastructure the "killer applications" leave in their wakes–but those include the PCI bus, Firewire, USB, Windows NT and Linux, Intel’s and
AMD’s variations on multi-operation instruction-set extensions, and MS-Visual C++.
With this wonderful, rich environment right in front of his nose, why would the application developer attempt to apply non-standard bits of technology, such as DSP boards, cameras with embedded processors, or pipeline processors? He does
so only because he must in order to meet immediate performance requirements, to meet non-computing requirements such as size or power supply restrictions, or perhaps as a matter of personal taste. (Some folks just love pipeline
processing!)
He knows full well that the PC, the two-ton gorilla of mass-market technology, will outstrip whatever non-mainstream technology he may pursue. It's just a matter of time.
For these reasons, in relative terms, we'll be right about where we are now in two to four years. Smart cameras will get smarter, DSP and pipeline processing components will get faster and cheaper (though alas, no easier to apply), but
PCs
will become vastly quicker and cheaper. PCs win strategically.
What will help us? Some machine-vision problems may take advantage of low-cost camera/PC interconnection technology developed for teleconferencing. Once PC motherboards routinely offer video inputs from low-cost cameras, the $400
board-level frame grabber disappears. But since every chip set and connector costs something, this won’t happen until enough homes and businesses have Web connections of sufficient bandwidth to support teleconferencing. That's one
reason we observe little adoption of Firewire for machine vision so far, even though some beautiful cameras are available.
John Hotchkiss, Data Translation: Despite the improvements in technology, my view is that the majority of the imaging market will continue to remain responsive to a simple solution: standard analog cameras using relatively
inexpensive frame grabbers in PCs.
Within that framework, development tools and application software are key, enabling users and integrators to tailor solutions more closely and quickly to the customer’s needs. One wrinkle on this is our DT3133 frame grabber, in which we
have packed three independent analog frame grabbers on one low-cost board. We have had a tremendous customer response
to the DT3133, precisely because it offers a lot of proven technology in a small space and at very low cost.
Richard Jaenicke, Mercury Computer: Despite the increasing image processing performance of mainstream PCs, Mercury sees the use of image-processing boards actually accelerating. This demand comes from applications that in the past
could only be solved through custom solutions but now can now be implemented cost-effectively using off-the-shelf, high-performance image-processing boards. In the embedded space, we also see these image-processing boards maturing
to take over some or all of the functionality of the host systems.
The availability to meet these demands comes from new technology that has changed the balance between hard-coded and programmable solutions, such as the addition of vector processing units in standard microprocessors, such the AltiVec
technology used by the PowerPC 7400. AltiVec provides Giga-ops of image processing performance that can be easily accessed from a standard C or C++ programming environment.
Another technology that is driving the change is the availability of embedded data switching that meets the requirement for high bandwidth with a low cost. One example is the ANSI standard RACEway crossbar switch. RACEway allows multiple
high-bandwidth data streams to be switched in real time. This is particularly important in systems that have high-bandwidth data sources or systems that require data sharing to solve latency problems.
Marc Damhaut, Euresys: I don't think that we’ll see big changes within the next four years. The standard PC platform
will continue to offer the best price/performance ratio, so PC-based systems (meaning PC + frame grabber + camera) will remain a good solution for many applications. For applications requiring high data bandwidth, the use of an image-
processing board (including image pre-processing and/or data reduction) will remain important. Video surveillance is becoming an important market as security companies realize that a PC can replace a VCR!
John Morrissey, MuTech: Users have always been looking for an interface between video and the computational power of the computer. Cost has always been a factor as well. In looking at the alternatives, you still need to look at the
performance required, and the cost of the solution. While 1394 and other serial digital interfaces, stand-alone boxes and smart cameras make sense in certain applications, the least expensive solution with the performance required over
the next two years will
be dedicated frame grabbers. Beyond two years, the digital interfaces/digital cameras will replace dedicated analog frame grabbers, but it will be driven by components and standards coming out of the consumer marketplace.
Which will stay board-based?
Barry Mazor, Advanced Imaging: Do you all see defined, different imaging market sectors or apps as most likely to choose board-based approaches longer—and if so, which ones? And while we’re at
it—why?
|
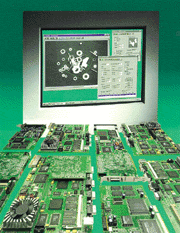
George Blackwell, Cognex: There are some market sectors such as pharmaceutical that will prefer image-processing boards or packaged vision systems where there’s a high cost of validation and they want
systems that are stable over long periods of time.
Also, automotive companies tend to prefer image-processing boards and packaged systems for their lower life-cycle maintenance costs. Systems integrators will prefer frame-grabber-based solutions that they can develop with their own
software, as will certain types of OEMs seeking the lowest possible cost options.
Pierantonio Boriero, Matrox Imaging: Medical imaging applications such as ultrasound as well as machine-vision applications that require high-resolution and/or high-speed frame or line-scan cameras will need to use the
frame-grabber approach for longer. Machine-vision applications that work with TV data rates will tend to migrate to high-speed digital serial buses sooner. For image processing boards, applications such as wafer inspection, web
inspection, and medical X-ray will require this approach for longer.
Tony Molinari, Foresight Imaging: We see the medical imaging market to be continuing to utilize board-based approaches for a number of years for a few reasons. First, the medical imaging market offers a more
diverse set of video formats than any other video industry. Historically, we've seen many non-standard video formats up to 150 MHz in the medical industry, and we have just recently seen one at 180 MHz. Board-based solutions are essential
for solving these wide-ranging video needs.
Second, there is an enormous amount of "legacy" equipment in the world that requires interfacing to the newer, and more expensive DICOM-based digital systems. The medical industry and its specialized video formats also re-quire
tight integration between software and hardware in order to enable quick and easy solutions for medical technicians and doctors. That’s why, for example, Foresight Imaging’s Auto-SYNC automatic configuration software, coupled with our
I-Series or HI*DEF hardware, are designed to automatically analyze the incoming video signal and configure the board
for precision image acquisition or streaming.
That means that what could take conventional frame grabbers several hours to accomplish (if at all), a medical technician
can interface to several different medical modalities in a hospital in a matter of minutes.
Phil Colet, Coreco: Certainly, there is a trend in the market place towards less proprietary solutions. OEMs are not willing or able to adopt solutions which remain static, rather, they must select solutions which continue to grow
to meet their increasing demands.
Additionally, and to remain consistent with the first question, these OEMs are looking for systems which do not require a massive software re-write. As an example, the semiconductor inspection industry had a requirement in 1998 to process
data at rates of 100 MB/sec. Currently, these rates have increased to 300-400 MB/sec and are expected to exceed 800 MB/sec in the next two years. That is an eightfold increase in data in just four years. These OEMs must adopt platforms
which can grow with their requirements, and they are likely to look towards board-based approaches.
John Morrissey, MuTech: It would seem that the security marketplace, both video and ID, would adopt the 1394 interface sooner. Compressed video from 1394 cameras and the lack of real-time control requirements in the applications
allow the technology to be implemented with relatively inexpensive cameras. Applications that require some type of real-time control will still need dedicated interfaces.
John Hanks, National Instruments: NI sees two broad classes of customers wanting the benefits of PC-based platforms that include vision, motion control, and data acquisition. These customers include measurement professionals and
machine builders in many market segments–semiconductor, biotechnology, and fiber optics. NI sees production test and measurement end-users who, in the past, measured signals such as temperature, vibration, current, voltage and so on are
now embracing images or vision as a mainstream measurement and test technology. These customers are very interested in open, PC-based solutions in which they can integrate many types of diverse I/O. And they are interested in easy-to-use
software that integrates this hardware such as LabVIEW and Visual Basic.
We also see exploding growth in two emerging market segments–R&D labs that test and develop material science and fiber-optic products. Companies are now moving these products from the lab into production. For example, companies are
using PC-based vision, motion control, and data acquisition to automate combinational material science, build thin-film machines, and to align, cut, and fuse
fiber.
John Hotchkiss, Data Translation: A potential machine-vision customer will generally not want to go with bleeding-edge technology over a simple solution that has been proven in similar environments. If the simple solution does not
perform the task, only then will the customer explore new technology until the solution is found. But I think that most customers across the market spectrum will stick with board-based solutions until a less-expensive, highly-flexible (or
highly-targeted) non-board-based system arrives. I am not convinced that that has happened yet.
Marc Damhaut, Euresys: In two words: machine makers (i.e. OEMs). Machine makers need processing power at low "duplication" cost. They can afford a slightly longer development time than one-shot applications makers
can. They have software and hardware engineers who can integrate a frame grabber and write application software based on vendors' low-level libraries.
Brad Finney, Imaging Technology: I believe that the machine-vision and high-end image analysis markets will stay with a board-based approach. The more challenging applications are forever pushing the limits of our capabilities. For
example, vision companies are constantly coming out with products that will handle new types of cameras with higher resolutions and speeds that the non-board-based approach won’t be able to adjust to as easily. I do, however, believe
that the lower-end applications should gravitate toward the PC's integrated vision solutions because of the cost benefit.
Richard Jaenicke, Mercury Computer: Mercury's image- and video-processing business has been targeted at applications that require the higher performance afforded by board-based solutions. This covers a wide range of applications in
medical imaging, such as digital X-ray and 3-D imaging, in defense applications such as electro-optic, infrared, and hyperspectral imaging, and in high-end industrial applications such as inspection of semiconductors, postal packages,
and other 3-D objects.
Jeff Wilson, Bitflow: Acquiring "exactly the images required" means response to real-time events such as triggers or
shaft encoders, and initiating real-time events such as strobes or laser flashes. Since the mass-market applications like teleconferencing aren't fussy about capturing particular images, it's not reasonable to expect PC motherboards to
include real-time event-control hardware. The job falls to manufacturers of camera interface boards. It's their business.
So, if you manufacture camera interface boards and wish to make money, look for applications that are both feasible given today’s PC I/O and computing capabilities and require precise real-time control of external events, not just
acquisition from free-running cameras. You get paid for this because you add value, and you stay out of the way of the two-ton gorilla. Good example: 900 Hz frame-sequence capture synchronized with strobe illumination. Bad example: video
surveillance! Another bad example: Computing FFTs (Fast Fourier Transforms) as part of a real-time image-recognition algorithm. Understand: There is nothing bad about these applications, they are just not likely to help you put your kids
through Harvard if you manufacture camera interface boards!
What technologies will have the greatest impact?
Mazor, AI: What changes in on-board, on-computer hardware or, for that matter, other related oncoming technologies, do you expect to see impacting board capability most—and how?
|
Phil Colet, Coreco: There are two technologies that I see will have the biggest impact on upcoming board capability for machine-vision applications. The first is Field Programmable Gate Arrays (FPGAs) as
they continue to increase in gate density and the software tools used for programming continue to improve. Coreco uses FPGAs on its own Pixel Processor to process data at rates up to 160 MB/sec.
The second is the use of embedded technology for imaging applications. In this realm, there are two product offerings: the embedded Pentium III from Intel (embedded and therefore offering low power dissipation in a slim line package) and
the embedded Windows NT operating system (offering developers a software compatible environment to the host computer). Both technologies will be available on Coreco’s next Mamba platform.
John Hanks, National Instruments: National Instruments has been using FPGAs for several years now, as a core technology on our vision, motion control, and data acquisition hardware. Today, our products use this technology to speed
alignment of data and to handle low-level image acquisition processes. For example, we’re leveraging this technology to reorganize on-the-fly the data coming from multiple-channel digital cameras or to provide our customers with a color
frame grabbers capable of acquiring and converting color image to HSL color space in video real-time.
In addition, we see technologies such as Camera Link simplifying how users can connect their industrial digital camera to a PC. In the past, there has been no standard for digital camera cabling which has created incompatibility between
cameras and image acquisition devices. IEEE-1394 for image acquisition, motion control and data acquisition is another technology to watch.
Richard Jaenicke, Mercury Computer: We see the two main changes in technology coming in the types of processors that are used and in the connections between boards and between
processors. Instead of adding ASICs to DSP chips, image- processing boards will add FPGAs to microprocessors with added vector-processing capabilities. The communication between all of the processors and the rest of the system will
eventually move to a widespread embedded switched fabric interconnect. Together, these two changes will provide balanced increases in system performance.
Pierantonio Boriero, Matrox Imaging: The emergence of standard high-speed digital serial computer interfaces such as IEEE-1394 and USB 2.0 will replace traditional frame-grabber boards with bus adaptor boards (or nothing else if
they are directly integrated into the host computer). However, these external buses are not yet capable of handling the data throughput requirements encountered in all imaging applications. New host computer architectures featuring IA64
processors and the PCI-X bus may limit the use of dedicated image-processing boards in the lower end of the application spectrum. However, this remains to be seen.
George Blackwell, Cognex: One thing will be more intelligence in the camera, which may include I/O and/or image pre-processing. This will offload processing from the main image-processing board. Digital acquisition removes the need
for any A/D conversion on the vision board. Potentially, in the four- to five-year time frame, there may be a standardized digital link for PCs like a future USB or IEEE-1394 spec that has enough bandwidth and control capability for
machine vision image acquisition.
Tony Molinari, Foresight Imaging: In the industrial imaging market, we see some of the newer (and not so new) digital interface technologies affecting board design and capability, including Firewire, USB, and Channel Link. New
digital technologies can take a very long time to be dominant–or even prevalent–in the marketplace, especially the industrial market. Take Firewire. Firewire cameras were first introduced in the autumn of 1995 in the prosumer market
for video editing and multimedia applications. This technology had not become prevalent in those markets until the last year or so.
We should expect a similar length of time for this to occur in industrial imaging, so we still have a few more years before prevalence takes place.
Further, in industrial imaging, we see a decreasing need for processor-based imaging boards due to the ever-increasing speed of CPUs, the CPU's easy programmability, the decreasing cost for more computer-based processing power, the
difficulty of programming on-board processing products, and the increasing availability and decreasing costs of multi- processor based computers. In the medical imaging market, we see the introduction of newer medical equipment and
technology requiring higher and higher acquisition frequencies, perhaps even over the maximum of 180 MHz that we
have currently experienced.
John Hotchkiss, Data Translation: I see the new PCI bus as being important to frame-grabber manufacturers, among others. This will open up new opportunities in the high-end board market. Additionally, Firewire and USB 2.0 offer
some limited, though interesting, opportunities.
Marc Damhaut, Euresys: New standards are emerging to simplify digital camera connection. This is a must. Users are looking for a plug-and-play camera solution and, so far, this
has been very painful for us frame- grabber manufacturers. The PCI bus will get faster and faster, along with PC processors, allowing more and more data to be transferred and processed inside the PC environment. And users are now looking
for frame grabbers to be able to control and acquire images from several cameras simultaneously. This is emphasized by the limited number of PCI slots and the increasing processing power of the PC.
Brad Finney, Imaging Technology: The Intel architecture, unfortunately, is effectively capped in potential, due to the number of processors that can be effectively used in a machine and because of the PC memory architecture. This,
coupled with the constant thirst of customers for more processing capability, has opened up the market for vision boxes and given new life to board-level products with on-board processing. I believe there will be an excellent market for
these products in the next 2-4 years. The increasing speed of the Intel processors themselves is not enough to stem this trend. If Intel were to deliver a usable multiprocessor architecture (including a non-global memory system), this
whole dynamic would change.
Jeff Wilson, Bitflow: At this moment, we're nearly back were we were in 1992-1993 in relative terms! At that time, high- end cameras had outstripped the PC's ISA bus ability to absorb real-time image data. Back when BitFlow
introduced Raptor, it let the PC keep up with cameras that were generating image data at the (then) blistering rate of as much as 17 MB/sec. Relieving the I/O bottleneck obsoleted quite a few ISA-based products with big on-board memories,
DSPs, and pipelining chips.
Our introduction of the Road Runner and Raven digital and analog camera interfaces families, which take full advantage of PCI bus capabilities to move pixels directly into virtual memory at rates better than 100 MB/sec while consuming
about five percent of the PC's CPU. But it's still not enough. It's never enough.
Another trend driven by the camera manufacturers impacts the board companies: shrinking cameras. All things being equal, customers prefer the smallest camera available–which is at odds with the need to bring signals in and out of the
camera using practical connectors. The solution on the low end is the unprecedented agreement between Dalsa, Basler, and Pulnix
to adapt National Semiconductor's Channel Link to the problem. Fiber-optic cable might seem the ultimate solution, but terminating fiber in connectors is difficult. Besides, practical cameras for machine vision require two-way,
full-duplex, real-time communication for the reasons stated above.
Channel Link offers a decent compromise. It time-multiplexes several relatively slow signals into a single copper differential signal pair, then de-multiplexes them at the receiving end. Based on good old LVDS, a camera interconnect that
incorporates Channel Link can offer thinner, lighter cabling yet offer as many non-muxed, bi-directional real-time control lines as might be required.
Where is your company headed?
Barry Mazor, Advanced Imaging: If you’re willing, tell us a bit about the directions you see your firm’s hardware taking over those next 2-4 years to take these technology and market changes
we’ve been discussing into consideration.
|
Phil Colet, Coreco: Given the seemingly conflicting goals of processing rates increasing to 800 MB/sec and beyond, reduced time to market and software investment preservation, Coreco has adopted a long-term
product introduction strategy designed to meet all of these goals.
First, by adopting an embedded Wintel platform, Coreco is able to continuously offer faster processing rates, simply because the clock rates of Intel's processors are increasing quarterly. Coreco will also be introducing an Intel solution
which will double the performance of previous solutions. The great advantage to OEMs is that these solutions do not require any new software–the advances are software-transparent.
Coreco will also be introducing advanced versions of the Pixel Processor utilizing the latest in FPGA technology extending the capabilities of the platform to 800 MB/sec. Since the processing core of the FPGA lies under a standardized API
layer, the OEM does not need to re-develop any software resources in order to leverage the power of the model.
George Blackwell, Cognex: In the past, it was important for a vision system to work within a PC architecture. In the future, it will be important for vision systems to work within a networked environment. Some vision systems will
continue to be PC-based, but there will be an overall trend toward packaged vision systems that communicate with multiple devices over
a network. The result will be more distributed processing and less overall dependence on the PC environment.
Pierantonio Boriero, Matrox Imaging: Our frame-grabber line will continue to evolve to meet the ever-increasing performance of cameras with traditional interfaces while the industry waits for faster standard digital serial computer
interfaces. Our image-processing board line will also continue to evolve in order to offer processing power and data throughput superior to upcoming host computer platforms. Our new stand-alone vision box and established software
lines will be developed to meet changing platform requirements for imaging applications. In fact, more than half of our development effort is now focused on software.
Tony Molinari, Foresight Imaging: We'll continue to focus on our customers' needs in medical imaging and industrial imaging. These include designing the highest-accuracy frame grabbers and video streamers and delivering the images
and video streams at the highest possible rates for system-based processing. We see our customers requiring video streaming
at higher video rates and we see an increasing need for the newer digital input technologies.
We also see a need to interface to higher-frequency video signals in the medical world. We plan to address these needs
by continuing to focus on our I-Series architecture and our Auto-SYNC automatic video configuration software platform. Just as important, we will place no resources on on-board processing products. As I said above, we see the need for
those products further diminishing due to programmability, time-to-market, costs, and the increasing speed and decreasing costs
of CPUs and multi-processor based computers.
John Hotchkiss, Data Translation: We will be aggressive in reaching out to potential customers with unmatched machine-vision and scientific-imaging software supported by appropriate hardware and support. The form the hardware takes
depends upon market requirements. We are focusing on solutions and will continue to produce hardware to support the overall solution.
Brad Finney, Imaging Technology: Our hardware direction is rather simple–even though it is still a ton of hard engineering work! It is our plan, in general, to stay with the board-level strategy. The challenges are these: keep up
with
new camera technology (speed, format, bit-depth, etc), keep up with new computer technology (AGP bus, fast and/or wide PCI, etc.), keep cost reducing our boards where possible, add value to our boards where possible (on-board processing,
I/O, etc.). There is a moderate trend to remove the vision task away from the host processor and we will capitalize on that trend with vision boxes and boards with on-board processing. The final goal for our company is to provide the best
support
in the world to make these board-level technologies as easy to use as possible.
Jeff Wilson, Bitflow: Those leading camera manufacturers are now offering machine-vision cameras that are capable of spewing forth pixels at 200 MB/sec, and output rates approaching 800 MB/sec are under consideration. So,
foreseeing this trend, BitFlow had already built a synchronization bus into the Road Runner–and now has demonstrated 200 MB/sec camera interfaces using two synchronized RR boards. Certain mother-boards designed for web-server apps
(There's that two-ton, mass-market gorilla again!) provide two independent PCI paths into PC main memory, each capable of 100 MB/sec throughput. But we know that a factor of two doesn't last long in the technical computing world. We’ll
need factors of eight or ten.
Marc Damhaut, Euresys: Euresys is definitely investing in the new Camera Link standard. Cabling problems are currently a major cause of problems for industrial users using digital cameras. The new Camera Link standard will be the
solution. Multi-point inspection (control and acquisition from multiple cameras) is a key advantage of our EureCard Multi (for digital cameras) and will be supported by our new EureCard Domino Gamma (for analog cameras). DSP or FPGA based
image-processing boards are mandatory when the data flow is too fast to be transferred to PC in real time. Euresys offers solutions with the Multi Plus and Multi Express. We also focus on very-low-cost frame grabbers (the Picolo series)
for specific markets, such as video surveillance.
John Hanks, National Instruments: Companies who follow National Instruments technologies and products closely
can easily forecast our direction. Over the last year and a half, NI has released many new real-time data acquisition and instrumentation products based on LabVIEW software and the PXI/CompactPCI measurement and automation platform.
Machine builders are using this platform in a wider range of semiconductor, fiber-optic, and biotechnology process control and monitoring applications. NI sees
many opportunities for real-time and embedded applications with software such as LabVIEW. The second area is networked measurements and automation. NI will continue to grow our product offering for image acquisition, motion control, and
data acquisition products with network connectivity.
John Morrissey, MuTech: MuTech targets applications in industrial vision, security, medical imaging, and image analysis and will be developing products and video interfaces that address the specific requirements of OEMs in these
areas.
Richard Jaenicke, Mercury Computer: Mercury’s products will incorporate FPGAs in addition to AltiVec-based PowerPC microprocessors in order to provide reconfigurable computing for various repetitive tasks such as performing
convolutions of various sizes. This combination will provide both the performance and flexibility needed to get to market more quickly. Processors and devices on the same boards and between boards will be connected first by RACEway and
later by RapidIO to provide the throughput and low-latency for high-end image processing. At this point, the image-processing boards and the host become peers, and the functionality of these sophisticated systems will be accessed through
more powerful software frameworks based on real-time, embedded CORBA.
Back to top
|